Fashion Design Undergraduate at Missouri State University
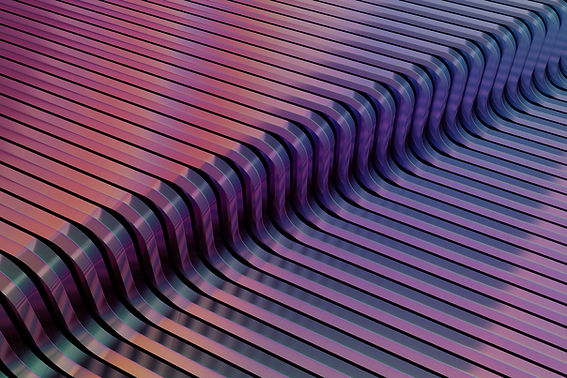
3D Fabrications
3D Fabrications is the study of 3D modeling and printing, laser cutting and engraving, and CNC milling. These are intricate and advanced ways of constructing a garment that I explored during my time at Missouri State University. I focused on how 3D printing can elevate the garment construction process.
Art In Bloom: A Study of Pythagoras By Linda Howard
I was invited to participate in the Art In Bloom event put on by the Springfield Art Museum. The event was to create a fashion look inspired by one of the Springfield Art Museum's pieces- I chose Pythagoras by Linda Howard. I also used this event as an opportunity to explore different ways that 3D Fabrication techniques can be used in Fashion. This particular look was created by printing PLA filament onto tulle fabric (Details discussed below) to combine 3D Fabrications with the traditional Garment Creation process. This look won Best In Show and secured me $1,000 of prize money. Garment was drafted using traditional draping techniques, and was constructed by layering each panel with a Crepe-Back Satin lining, a Medium-Weight Cotton Twill Weave face fabric, and the 3D printed Tulle layer. Neckpiece was constructed by melting the backs of the PLA printed pieces together to create the illusion effect.



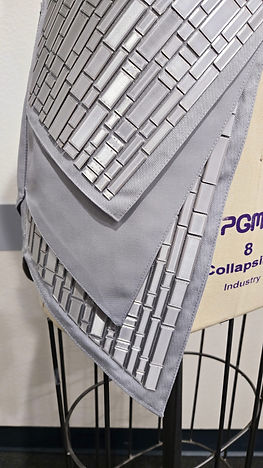





Finished photos of my completed Art in Bloom Submission.
A Detailed View Into the 3D Fabrication Process
Step 1:
Drafted and Digitized all pattern work in Adobe Illustrator. Kept verifying all necessary measurements to ensure accuracy and precision when printing. Made sure to transfer all markings and grainlines during this step.
Step 2:
Defined the geometric repeat. Then tiled the repeat across my digitized pattern in Adobe Illustrator to prepare the file to be imported into Rhino. Made sure that the repeat had a fill but no stroke to ensure proper import into Rhino.
Step 3:
Took the tiled repeat and pattern pieces to create the 3D model. This is done by using Rhino to extrude the curves made in Illustrator and then using various Boolean functions inside of Rhino to achieve the desired model.



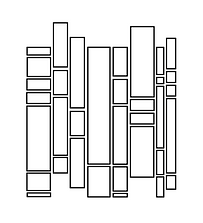
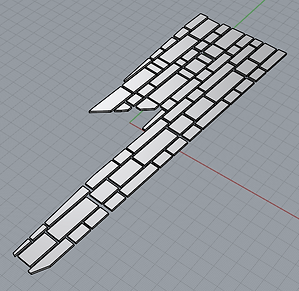

Step 4:
Sliced the 3D model in Cura to prepare for printing. I added a Post-Processing Script to my G-Code file to pause the print after its second layer. When it paused, I went in and taped down a layer of tulle fabric, and then restarted the print. This allows the layers to melt together through the tulle and create a strong bond.

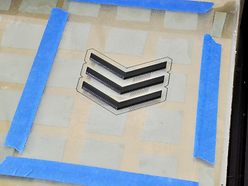
In-Progress Screenshots of the 3D Fabrications process. Includes photos from Adobe Illustrator, Rhino, and Cura.
Designer Statement on Display at the Springfield Art Museum:
I was immediately inspired by Pythagoras by Linda Howard when I saw it. Seeing the repetition of the geometric lines, the subtle texture on the sides, and how the light and shadows of the windows behind it reflected on the sculpture at midday made the sculpture stand out to me. To interpret this piece I used several techniques. I used a structured twill weave to communicate sturdiness and rigidity, silver satin to communicate the play of light and shadow, and the 3-D printed repeat on tulle to mimic the texture and repeat on the side of the sculpture.
What I love the most about this sculpture is the repetition and how the viewer's eye is guided around the piece. I mimicked this in my own garment by using repeating lines and layers, as well as symmetrically placing converging geometric lines and pleating to create my perspective. The mixture of materials, the use of geometric lines that are either evident or implied, and my use of repetition creates the vision of what I see when looking at Pythagoras.
I hope you enjoy my interpretation of Linda Howard’s work and I believe the best time to view this piece is around midday when the lights are coming in from the windows, so you too can experience the play of light and shadow.

Pythagoras by Linda Howard; Metal Sculpture.
Resin-Printed Gothic Harness
Harnesses are part of my signature style, so for my first attempt at 3D fabricated fashion, I decided to make a harness inspired by gothic architecture. The harness features: specially designed O-Rings, a featured chest design, and a base plate that functions as the structure for the harness. It is made of 3D printed Ultra-tough Resin, 1" metal D-rings (for closures), and 1" nylon straps. When modeling the hardware in Rhino, I carefully followed the dimensions of O-rings I have used in the past to ensure function, and then added in my gothic-inspired designs around those specifications. For the Base plate, I modeled openings in the back to provide space for the nylon straps to loop through- thus creating the structure for the piece.

Editorial Photoshoot of finished harness. Photos shot by me.


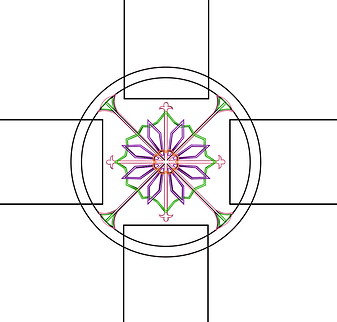

Starting Point of all pieces in Illustrator. I started drawing base concepts in Illustrator to import into Rhino. Final details and modifications were done in Rhino.








Detail Shots of 3D Models in Rhino. Pictured top to bottom: O-Ring Designs, Central Motif, and Engraved Base Plate.
Award Design for eFactory's Innovation Accelerator Event
I was selected for and produced the award design for the Innovation Accelerator Event at the eFactory. The prompt was to remain consistent with university branding while also exploring the Innovation concept. I fulfilled this prompt by including Missouri State University's logo into the lightbulb design. I made the base idea in Illustrator and then brought it into Rhino to make it 3D. I then modeled the base completely in Rhino to the specifications requested by the eFactory. The design went through several prototypes to decrease resin usage, speed up production times, decrease the amount of support needed, and to decrease warping during printing.
.jpg)
.jpg)
Cliff Smart handing off the award after the completion of the event at the eFactory.




Illustrator Vector File (before prototype changes); Collection of Renders of design (before prototype changes).
Modular Sculpture with Connectors
For my first 3D Fabrications project, I was tasked with creating a modular sculpture with at least three different connectors. I decided to use a coffin shape for the base and use pearl motifs in the connectors' designs. It was printed with PLA and was a test of accuracy within 3D modeling. All connectors were created and modeled in Rhino.

3D Model of Modular Sculpture in Rhino.
.png)
Finished Modular Sculpture with dowel rods and PLA connectors.